抽象から具体へ。“構造化”が変革の種
CASE①株式会社今野製作所
「何か問題があることはわかっていましたが、自分たちの力だけでは、その原因を特定することができませんでした。その状況を打開したのが、プロセス参照モデルです。これこそが、継続的な業務改善活動や本格的なIT化への取り組みといった社内変革を進めるきっかけになりました」
株式会社今野製作所の今野浩好社長は、リーマンショック後の経営危機を乗り越えていくことになった経緯をこう振り返った。
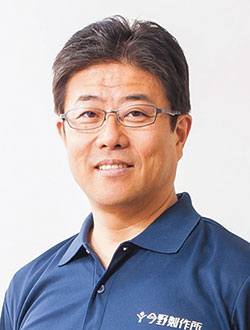
今野浩好社長
- 主な事業内容:
- 油圧機器製造・販売、板金加工等
- 本社所在地:
- 東京都足立区
- 創業:
- 1961年
- 従業員数:
- 37人
同社は、1961年に東京都北区で創業した。板金加工業からスタートし、76年には、後に国内シェア70%を占めることになる油圧爪つきジャッキ「EAGLE(イーグル)」の製造・販売に乗り出す。
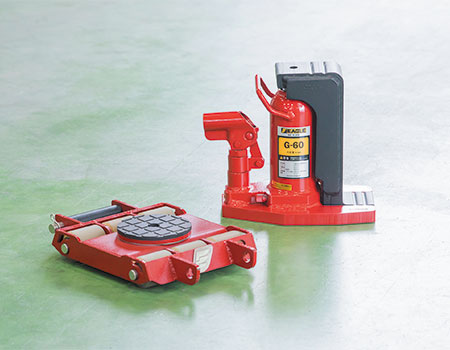
今野製作所の主力製品である油圧ジャッキ「EAGLE」。
最新の設計シミュレーション技術と、厳しい耐久試験に裏づけられた
品質は、日本のみならず、世界中のあらゆる現場を支えている。
両事業は堅調に成長していったものの、リーマンショックによって油圧機器事業が大打撃を受けた。同製品は重量物の運搬などに利用されるプロツールであり、その売上は世の中の設備投資と連動するためである。2008年の秋から売上が下がり始め、その翌年にはリーマンショック以前から45%も落ち込んだ。
「製造業で売上4割減となると、経費節減などをしても焼け石に水。しかも、すでに高いシェアを獲得していたこともあって、新規営業を頑張っても受注が急激に増えることはなく、回復の見込みは立ちませんでした。そこで、板金加工で培った技術を活かし、油圧機器の“特注品”に力を入れ、新たな需要を掘り起こそうと考えたのです」
顧客の細かな要望に対応した設計製造を行うことで、付加価値を高める戦略に舵を切ったわけだ。これによって新たな注文が入るようにはなった。しかし、受注数は月に1、2件ほど。売上回復には程遠い状況だったのにもかかわらず、なぜか社員の多くが残業するようになっていた
「オーダーメイドによる設計製造なので、従来品より業務が複雑になり、手戻りや工数が増えるのは当然です。しかし、そこまで数は多くないのに、社内は混乱していました。顧客の要求に応えてカスタマイズする営業は難易度が高く、設計部門に負担が集中。製造ラインもスムーズに回らなくなってしまっていたのです」
各部門の従業員で集まってミーティングを行ったものの、出てくる改善案は「日程管理をしっかりする」「業務確認の頻度を上げる」といった当たり前のことばかりで、効果はほとんど実感できなかったという。
藁にも縋る思いから、社外のあちこちで相談を持ちかけているうち、一人のITコーディネータに出会った。そこで今野社長が学んだのが、「プロセス参照モデル」だ。
「正直なところ、最初は、先生(ITコーディネータ)が話すプロセス参照モデルの内容をほとんど理解できませんでした。ただ、行動しなければ結果は出ません。せっかくの機会でもあったので、各部門の次世代リーダーたちで構成したプロジェクトチームを編成。丸1年、月に2回くらいの頻度で、業務改善活動をスタートしたのです」
問題の原因がわかれば、解決の道筋が見えてくる
プロセス参照モデルとは、「仕事=業務機能が連鎖することで成立しているもの」という前提に立って、粒度を揃えながら、社内の業務全体を階層別に構造化し、定義していく手法だ。各業務が持つ機能について、「インプット」「アウトプット」「方法・ルール・制約条件」「設備・人(技術・知識)」を明らかにすることで、業務不全の原因を探っていく。例えば、もっとも大きな括りであるレベル1では、生産、調達、出荷、設計などに事業要素を分類し、レベル2では、それをさらに細分化する。生産であれば、受注生産、見込み生産など、実施方式の違いごとに分けるのだ。このように、それぞれの業務を、レベル4まで分類していくことで、プロセスを徹底して可視化する。
全体の流れを把握したら、各担当者にインプット、アウトプットなどの作業を具体化してもらう。受注であれば、インプットは注文内容をパソコンに入力すること。アウトプットは、入力したデータを誰が使うのか、といった具合だ。
「この作業によって、自分の仕事には、どのような情報や材料が必要なのか、自分の作業の質が、他の業務にどのような影響を及ぼすのか、全体の業務フローのつながりの中で、自身の役割を理解できるようになります。加えて、コンサルタントと質疑応答を重ねることで、各部門の問題点もあぶりだされていきました」
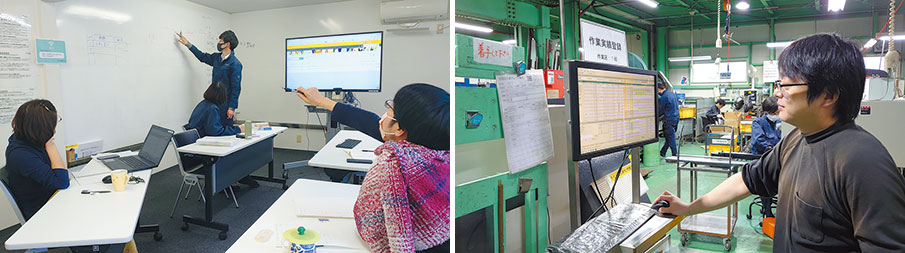
(左)各部門から意見を出しあいながら、全体最適の業務改善を進めていく。
(右)各現場で入力された情報は社内全体に共有され、スムーズな業務プロセスを構築している。
特注品の設計製造では、営業時に顧客と交わしたやり取りの記録が、設計担当者にとってのインプット情報になる。
しかし、これが十分に伝わらず、業務の手戻りやクレーム発生の原因となっていた。また、製造に必要な部品は、設計部門が作成したリストをもとに、購買部門が発注するものの、情報の流れが悪い、不十分などの理由で、手配遅れが生じていたことも明らかになったのだ。
「正式に発注されていないのに、営業都合で詳細設計まで進めているとか、オーダーメイドで設計したドキュメントに管理番号がなく、『〇〇社用の●●品』といった呼び方をしていました。そのため、設計者も何が何だか、わからなくなっていることもありました」
あぶりだされた問題点は、実に130以上。そのすべてについて、同時並行で対処するのはリソース的に無理だったため、もっとも優先度が高い、業務のスタート部分である受注までに絞り、ITを活用した改善に取り組むことにした。
「まずは、経験値でやっていた部分を誰でもわかる項目に統一化することによって、社内全員が把握できるようにすべきだと考えました。そのために活用したのが、Webデータベース型の業務アプリ構築クラウドサービスです。これを使って、引き合いから受注までの案件情報を管理・共有できる簡単なシステムを、あえて自社でつくることにしたのです」
これは特段難しいものではなく、半日もあれば完成するレベルだと今野社長は語る。
「特注品の仕様を把握するために必要な項目は、プロセス参照モデルによって明らかになっていたので、営業はお客様にヒアリングした情報を案件管理システムに入力。設計部門への依頼も、このシステムを通じて行うようにフローを変革しました」
案件管理システムに登録したもの以外の設計依頼は受け付けないとしたことで、「受注前だけど、とりあえず設計を始めて」といった変則的な要求を一掃。あわせて、技術担当者ごとの案件数も可視化し、特定の人に業務量が偏る状況もなくなった。
DXは、D(デジタル)でX(変革する)と解釈されるため、“何を”という目的意識が欠けた状態で進められることも少なくない。しかし、今野製作所では、はじめに変革すべき課題を見える化した。実はこの工程がもっとも大切で、その上で解決のための手段として、ITツールを導入する、いわば“XD”だ。ここに、DX成功の秘訣があるといえる。
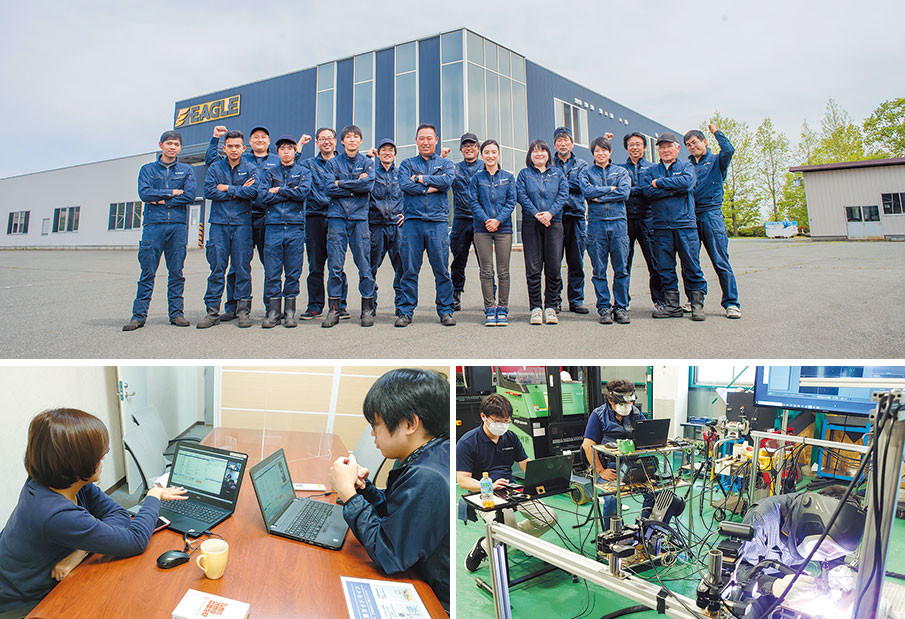
(上)業務改善活動は、油圧ジャッキを製造する福島工場に焦点をあててスタートした。
(左下)現在は、社内開発のシステムによって、東京本社とリアルタイムで連携している。
(右下)さらに、今野製作所では、溶接の様子をモーションキャプチャで撮影。
熟練技術者の動きと見比べることで、作業レベルの向上に努める。
システムを自社で開発し、継続的な業務改善を実現
こうして一つひとつの問題に対処していったが、プロセス参照モデルによって顕在化した解決すべき項目は、まだまだ山積みの状態だった。各所の課題を、市販システムの導入で対応するのには限界があると、今野社長は指摘する。
「例えば、生産系のシステムは多様な業態に対応するため、販売本数が少ない。そのため、小規模企業にとっては高額で、投資は容易ではありません。けれども、業務が複雑化している昨今、中小企業であっても、システムなしでは煩雑な作業をさばけなくなってきているのが実情でしょう。ここが“IT化の空白地帯”になっているのです」
同社では、こうしたDXの取り組みを長く続けていく中で、問題解決につながるさまざまなシステムを、独自開発していく道を選ぶ。
「ある大学教授を紹介してもらって、話を聞きました。その中で、情報には7つのムダがあると知ったんです。『必要な情報を探すムダ』『必要な情報の到着を待つムダ』『不要な情報を生成するムダ』など、こういった要因をコツコツと取り除くのが、情報連携の本質だと教えられました。また、業務システムを自分たちでつくることで、現場も、ともに成長していくことも気付かされました」
当時入社した技術系の新入社員を担当に指名し、外部の専門家によるサポートも受けながら、少しずつシステムを形にしていったという。
「生産管理システムからはじまって、在庫と受注、生産予定を確認できるシステム、油圧機器事業ではPSI(生産・販売・在庫)連携のシステムを最初につくりました。これは、福島工場にある製品の在庫数と受注数、生産予定を、東京本社からでもリアルタイムに確認できる在庫管理システムです。受注データは販売管理システムと連動させ、生産予定は工場の担当者が随時入力するようにしています。このシステムを確認するだけで、お客様から明日10台欲しいと問い合わせがあっても、すぐに回答できるようになりました」
自社開発したシステムの中には、約10年を費やして完成したものもある。それが、製品製造に必要な部品情報を管理するBOMシステムだ。設計データから必要な部品を表にして抽出すると、購入する際の価格と連動しており、一目で原価がわかる。
「手前味噌ですが、これはかなり有用なシステムで、営業も技術も生産現場でも使っています。これほどのシステムを自社開発できたのも、10年以上にわたって、IT技術を活用した改善活動をコツコツと継続してこられたおかげです」
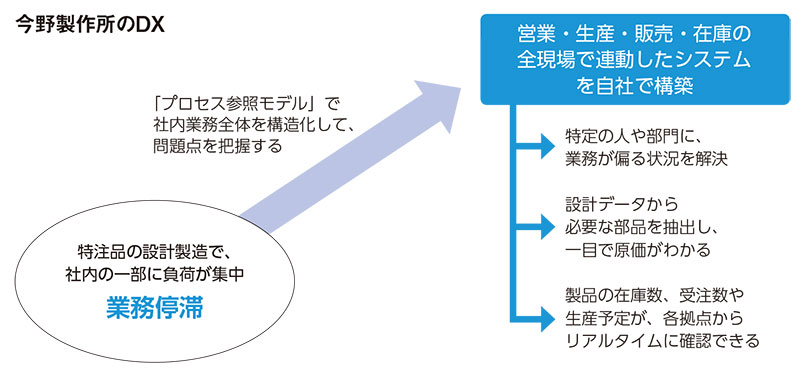
小さな成功体験が、大きな推進力となる
今野製作所では、プロセス参照モデルをもとにした業務改善活動を、現在でも継続して行っている。その結果、自社開発システムは20近くに達しているそうだ。業務システムを開発するためには、現場の協力が欠かせない。さらに、システムを改良していくには使用者のフィードバックが必須となるため、密な連携が必要だ。一体、どのようにして現場を巻き込んでいったのだろうか。
「最初の頃は、トップダウンで進めていました。変化が出てきたのは、4年ほど前からでしょうか。現場の声を書き込めるアプリを通じて改善提案などが寄せられるようになったのです。大切なのは、“現場が喜んで使うもの”をつくることです。現場の困り事や不便さを解決するシステムであれば、何も言わなくても活用してもらえるし、要望もたくさん出てきます。経営者目線でシステムを導入しようとすると、最大公約数的な機能や、一部の偏った意見だけで選びがちです。しかし、経験上、そういったものはうまく機能しません」
はじめから、多機能で高価なシステムを入れる必要はない。身の丈に合ったミニマムなツールでも、対処すべき課題が明確であれば、その効果は高く、現場も便利さを実感し、さらなる改善につながる。これを繰り返していくことが、DXを成功に導くコツなのだ。小さな成功体験の積み重ねが、システムも、それを使う従業員も、会社も成長させていく。
今野製作所は現在、こうした思いを同じくする製造業の2社と、業務連携や人材育成に挑んでいる。業界全体の変革を目的に、どのようなデジタルの道を歩むのか。同社の行く先から、目が離せない。
機関誌そだとう210号記事から転載