経営資源を集中、“やらない選択”のススメ
CASE①日本光機工業株式会社
ポートフォリオと聞くと、広い分野で異なる事業を複数展開しているような、大企業をイメージする経営者が少なくないだろう。しかし、自社のコア・コンピタンスを正しく把握したうえで事業ポートフォリオを策定し、上手に経営資源を分配する、もしくは集中すれば、会社や事業の規模に関係なく、レジリエンスの高い企業をつくることができる。
航路標識と航空標識を手がける特殊照明メーカーの日本光機工業株式会社は、“光の標識”というひとつのフィールドを、ニッチな市場でうまく展開している企業だ。現在では、海岸の灯台や港湾の信号、航空機の滑走路に設置する飛行場灯火や、建造物の存在を知らせる航空障害灯などの一部分野で、国内トップクラスのシェアを誇る。2019年に創業100年を迎えた同社だが、長い歴史の中では、競合他社が台頭した時期もあった。それでも、どの分野が伸びているかを常に考え、時代に合わせて経営資源を投下してきたという。長寿企業となった秘訣について、石崎康充社長はこう語る。
「100年以上成長し続けてこられたのは、市場の変化を見極め、ときには“やらない選択”をしながら、経営資源を集中してきたからこそ。その時代ごとにトップの分野をつくってきた結果でしょう」
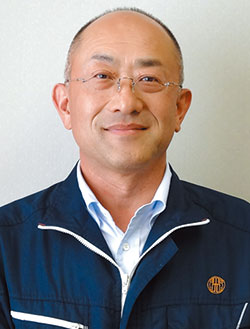
石崎康充社長
- 主な事業内容:
- 航路標識、航空標識の製作・販売及び関連する工事の請負
- 本社所在地:
- 神奈川県横浜市
- 創業:
- 1919年
- 従業員数:
- 71人
事業が上手くまわり会社の調子が良いと、背伸びをして事業拡大を狙ってしまいがちだ。また、ひとたび成功を収めた企業ほど、次への一歩は踏み出しにくい。日本光機工業はこうした難関を乗り越え、現在の地位を確立してきた。その背景には「官・民・海・空」4つの分野で、柔軟に軸足を移してきた実績がある。
ニッチ市場の中でも、柔軟な事業展開を実現
同社の創業は、第一次世界大戦終戦直後の1919年だ。すでに日本の海岸には灯台が普及していたが、戦争の影響で光を遠くに伸ばすレンズの輸入が困難になる。危機感を抱いた当時の逓信省技師が、レンズの国産化を目指して同社を設立した。
そうした創業の経緯から官との関係は深く、光学技術が軍部に認められることとなり、軍の指定工場となった。飛行機が飛び始めたことをきっかけに航空標識にも進出。32年、東京-福岡間の夜間航空路開設にともなって各地に航空灯台が建設され、その照明器具を製造したのが最初の案件だった。海、空ともに同社がパイオニアとなり、さまざまな光波標識をつくっていったという。
「会社が大きくなってくると、資金繰りの問題が発生しました。そこで安田財閥より援助を受け、その系列下に入ります。財務基盤が強化されたことでさらに成長して、一時は従業員2000人を擁する大企業になりました。工員養成学校を運営していたこともあったようです」
第二次世界大戦では空襲で壊滅的な打撃を受けたものの、戦後の国土復興でインフラ整備が始まり、航路標識や航空標識の需要が高まった。戦後復興期は、海も空も、国や自治体が発注者となる公共事業が中心だったが、当時は空路が未発達で、売上の7~8割は海だったという。
時代が進み、飛行機などの航空インフラが整備され始めると、航空障害灯のニーズも高まる。日本光機工業は47年に、日本第一号となる航空障害灯を東京と横須賀のガソリンタンクに据え付けた。都心の象徴である東京タワーの航空障害灯システムをすべて請け負ったのも同社だ。高度経済成長期で高層ビルが次々と建設されていく中、航空法における航空障害灯の設置義務を追い風に、民間の需要も伸びていく。しかし、日本光機工業は民間ビル関係をやらないと決断、最近まで本格的には参入していなかった。十分な技術も実績もあり、売上拡大を考えれば参入していてもおかしくはない。なぜ、そのような判断にいたったのだろうか。
「当時、ビル全体の屋内照明は、大手企業が一括納入していました。その流れで航空障害灯も安価で受注し、相場が下がっていってしまったのです。価格勝負では分が悪いと判断し、自分たちのフィールドである官庁に注力することを決め、技術や経営資源をそちらに結集させました」
これまで見てきたように、日本光機工業の事業は「官か民か」「海か空か」それぞれ二軸で4つの象限に分けられる。最初は“官×海”が中心だったものの、市場の変化に合わせて、主軸となる分野を臨機応変に変えてきた。同社が国内有数の航路・航空標識メーカーとして存在感を示し続けているのは、ニッチ領域でも複数事業を持つポートフォリオ経営を実現してきたからである。近年では、“民×空”に挑戦しているという。
「特に期待が高いのは、再生エネルギー関連です。風力発電施設に据え付ける航空障害灯では、トップシェアを誇るまでになりました」
これもまた、世界的な潮流をよく読み、会社の進むべき道を的確に捉えた結果だといえるだろう。
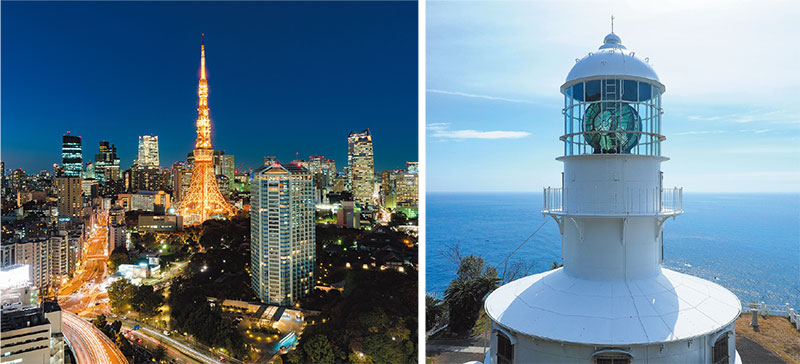
(左)都心の夜景を彩る東京タワーの光は、日本光機工業の航空障害灯。
1958年に同社が一括受注し、納入された。遠くからでも目立つ東京のランドマークとして、
電波塔の役目を終えた現在でも、多くの人に愛されている。
(右)高知県室戸市に設置されている「室戸岬灯台」。1899年に初点灯された同灯台は、歴史的価値を持ち、
「日本の灯台50選」のひとつにも選ばれている。直径2.6メートルのレンズは国内最大級。
毎年11月には「室戸岬灯台まつり」が開催されるなど、街のシンボルとなっている。
専業メーカーの強みで、競合他社に差をつける
さて、ポートフォリオ経営で事業の安定性が増したとしても、それぞれの事業でトップを取れるかどうかは別の話である。日本光機工業が各分野で競争力を高めることができた要因を、もう少し掘り下げてみよう。
同社が確固たる地位を築くことができたのは、専業メーカーの強みが関係していると石崎社長は分析する。
「競合は、一般照明器具や道路照明がメインです。定期的な製品見直しや認証などの負担が大きい割に、市場が小さい航路・航空標識領域のプライオリティーは必ずしも高くありません。その結果、他社では技術者を他の得意な分野へ振り分け、航路・航空標識に求められる特殊なノウハウの継承が難しくなっていると思われます。一方、私たちはこの分野の専業メーカーで、ヒト、モノ、カネを集中できる。自社工場を持ち、開発から生産、販売、アフターフォローまですべて自前でできるように投資し、体制を整えてきました」
こうした生産環境の差は、品質にも如実に表れる。日本光機工業が“民×空”に進出した当初、ひどい雷雨の影響で、同社製品を含め、風力発電施設で稼働していた航空障害灯の多くが破損。そんな中、試行錯誤の末に、いち早く有効な落雷対策をとった日本光機工業の新製品をつけた風車だけが、白く光を放ち続けたという。それをきっかけに「日本光機は落雷に強い」と風力発電業界で評判が広がり、今では陸上風力発電施設の航空障害灯の9割は、同社製品に切り替わっている。
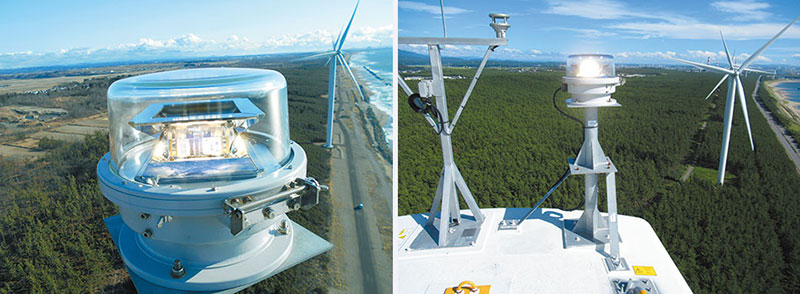
風力発電施設において、昼間でも航空機から視認できる白い光を放っている。
2001年に航空局より承認され、国内初の大型風力発電所である千葉県「銚子屏風ヶ浦風力発電所」、
北海道「花咲風力発電所」に設置された。
もうひとつ、要因として見逃せないのは、製品の認証ハードルの高さだろう。法律で設置が義務づけられている航路・航空標識の特殊照明は、明るさや色、点滅回数などの仕様も同法や関連法令で決まっている。その要件を満たし、行政に認められた機関の審査をパスした認証品であることが求められるのだ。
「航空障害灯の場合、まず国土交通省・航空局が定める国際規格に準拠した仕様に沿って製品開発を行い、指定された場所で夏、冬に供用試験を行います。世界各国の気象状況を踏まえて規格が制定されているため、暴風雨、極低温や高温多湿などの環境に加えて、塩害も考慮しなければなりません。開発を始めてから、各種試験を経て認証が下りるまで、平均2~3年はかかってしまいます」
たとえば、日本光機工業が開発した製品のひとつに、非常用滑走路灯がある。11年に起きた東日本大震災で仙台空港が被災。電源を必要とする滑走路灯が使えなくなり、空港の復旧に時間を要した。その教訓から、同社は乾電池式の非常用滑走路灯の開発に乗り出したが、認証試験を突破して、販売開始に漕ぎつけたのは18年。震災から7年かけて、ようやく日の目を見た。安全を司る製品のため、開発や認証には、それ相応の時間と労力、コストが必要なのだ。
さらに航空標識は、同じ製品をどこでも使えるわけではない。たとえば成田、関空、中部は、各空港での運用やメンテナンス方法の違いから、求められる仕様が異なり、それぞれで認証をとらなければならない。こうした細かなルールも、新規参入を阻む障壁となっており、柔軟な対応ができる同社の開発・製造体制も優位性につながっているという。
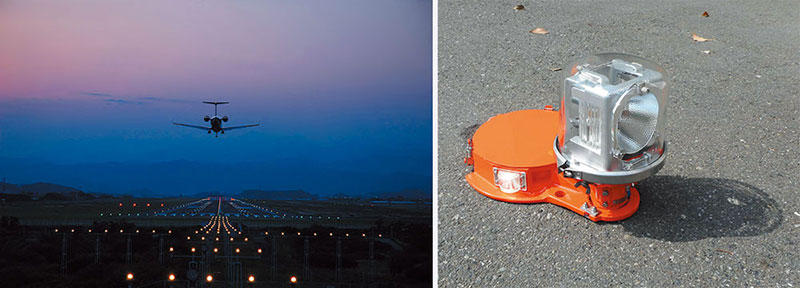
(左)旅客機の窓から見える、規則正しく並んだ飛行場灯火。空港における、飛行機の安全な離着陸を支えている。
(右)電源を必要とせず、単一電池8本で稼働する非常用滑走路灯。東日本大震災で被災した空港の経験をもとに、
緊急事態のときに飛行場がいち早く復旧できるよう開発された。
4つのマトリクスで、必ずどこかに需要がある
すべて自前でできる体制は、環境変化への対応力にもつながるという。現在、コロナ禍の影響で、製造業は半導体・部品不足に苦しんでいる。部品が調達できないと、通常は生産調整するか、代替品で設計し直すしかない。当然その分、コストも時間もかかる。しかし、石崎社長は「当社には開発部門があるので、すぐに設計変更ができる」と自信満々だ。
「工場には深さ8メートルにおよぶ耐水試験用の水槽や、最大で長さ50メートルになる暗室があります。こうした設備があると、自社内で試験をして、結果を迅速に開発に反映することも可能です」
柔軟な対応ができるのは、1~2年の短期変化に対してだけではない。むしろ注目すべきは、10年単位の長期変化だ。一般論として、ある技術で成功を収めた企業は、成功体験にとらわれ、次世代技術への切り替えが遅れることがあるといわれる。いわゆるイノベーションのジレンマだ。
日本光機工業はこの課題を常に克服してきた。創業当初のガス灯を使った灯台から、白熱灯への技術革新に乗り遅れることなく対応し、交換回数を少なくする機構の開発など、技術を磨いていく。そして80年代には他社に先んじて、いち早くLEDを取り入れ、実用化を進めていった。
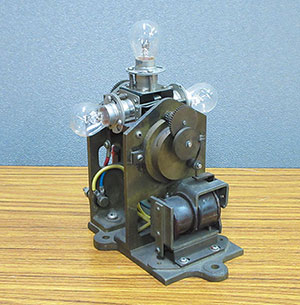
電球の交換回数が、なるべく少なく
なるよう工夫された「電球交換器」。
半導体がない時代、ひとつの明かりが
消えると磁力で検知し、予備球に切り
替わるよう設計されている。
当時のLEDは光が弱く、1個あたりのコストも高い。採算が合わず、製品化には苦労したという。
「離島の灯台などは、電球の交換が簡単にできず、電源の確保も困難。長寿命、省エネ、小型軽量のLEDは、絶対に需要があるはずと、粘り強く開発を続けました」
先に実用化に漕ぎつけたのは海の領域だ。88年、世界に先駆けてLED海上標識を神戸港に設置。さらに97年には日本初のLED航空障害灯が航空局に承認され、製品化した。
「海のLED化は、約20年前にだいたい終わっています。いまは官の飛行場や民の送電鉄塔など、空のLED化を進めるタイミング。一巡した海の方も、いまちょうど更新需要がきているところです」
石崎社長の話からは、ポートフォリオ経営が上手くまわっていることが伺える。LED自体も進化を続けて、より高性能なパワーLEDを使った製品の新設・更新が進む。従来製品はLEDの寿命が約2万時間だったが、パワーLEDの寿命は約4万時間と倍になっている。長寿化すれば更新頻度は減り、同社にとっては機会損失につながってしまいそうだが、その心配はいらないようだ。
「『官・民・海・空』どこかの領域だけなら、次の更新需要が待ち遠しいと感じるかもしれません。しかし、私たちは4つのマトリクスすべての分野で事業を展開しています。どこかの更新需要がひと段落しても、別領域で更新需要があり、また、新たなニーズを見据えた開発も並行して行っているので、問題ありません」
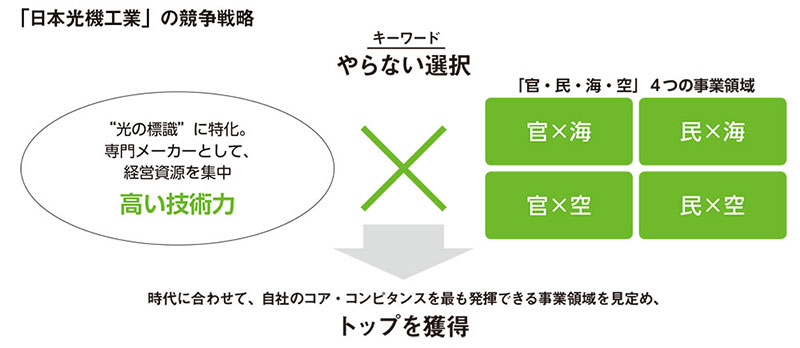
短期の環境変化、長期の技術トレンドに合わせ、“やらない選択”をしながら、ホットな領域に経営資源を集中する。その柔軟な姿勢が、日本光機工業をトップたらしめるのだ。
機関誌そだとう209号記事から転載